精益化生产管理:优化生产流程的关键
精益化生产管理是一种管理方法,旨在通过最大限度地减少浪费,提高效率和质量,从而实现生产流程的优化。它是从丰田生产系统中发展而来,如今被广泛应用于各种行业,包括制造业、服务业和医疗保健等。本文将深入探讨精益化生产管理的原理、方法和实施步骤,并提供一些建议,帮助企业实现生产流程的精益化。
精益化生产管理的核心原理是通过消除各种形式的浪费,实现生产过程的精简化和优化。这些浪费包括:
- 过剩生产:生产过多的产品,超出市场需求。
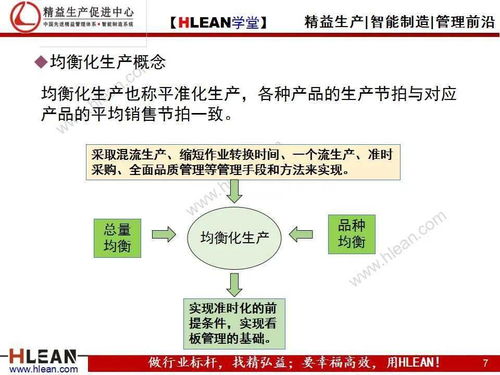
- 等待时间:生产过程中的停滞和等待,浪费了宝贵的资源。
- 运输:不必要的物料运输,增加了成本和时间。
- 过程缺陷:生产过程中的错误和缺陷,导致资源的浪费和重复工作。
- 库存:过多的库存占用了资金和空间。
- 运动:不必要的动作和移动,增加了生产过程的复杂性。
- 过度加工:对产品进行不必要的加工和处理。
通过识别和消除这些浪费,企业可以实现生产效率的提高,成本的降低,质量的提升,从而增强竞争力。
要实现精益化生产管理,企业可以采用以下方法:
- 价值流映射:分析生产流程,识别价值流和非价值流,找出生产过程中的瓶颈和浪费。
- 流程优化:通过重新设计生产流程,消除浪费,提高效率。
- 小批量生产:采用小批量生产和及时制造,减少库存和等待时间。
- 精益生产工具:使用精益生产工具,如5S、Kaizen、PDCA等,持续改进生产流程。
- 员工参与:鼓励员工参与精益化生产管理,发挥他们的创造力和经验。
- 供应链管理:与供应商和客户紧密合作,优化供应链,减少浪费。
要成功实施精益化生产管理,企业可以按照以下步骤进行:
确定目标:明确精益化生产管理的目标和期望效果,制定具体的指标和计划。
培训和教育:对员工进行培训和教育,使他们了解精益化生产管理的原理和方法。
价值流映射:分析和绘制当前的价值流图,识别并标记出各种类型的浪费。
流程优化:基于价值流映射的结果,重新设计和优化生产流程,消除浪费。
实施改变:在生产现场实施改变,包括改变工作布局、改进设备、培训员工等。
持续改进:建立持续改进的机制,定期评估和审查生产流程,寻找进一步的改进机会。要实现精益化生产管理,企业可以考虑以下建议:
- 领导支持:确保公司领导层对精益化生产管理的重要性有清晰的认识,并提供必要的支持和资源。
- 文化转变:培养精益化生产管理的企业文化,鼓励员工参与持续改进,建立团队合作精神。
- 重视培训:投资于员工的培训和发展,提高他们的技能和意识,使其能够积极参与精益化生产管理。
- 注重绩效评估:建立有效的绩效评估体系,对精益化生产管理的效果进行监测和评估,及时调整和改进。
- 持续